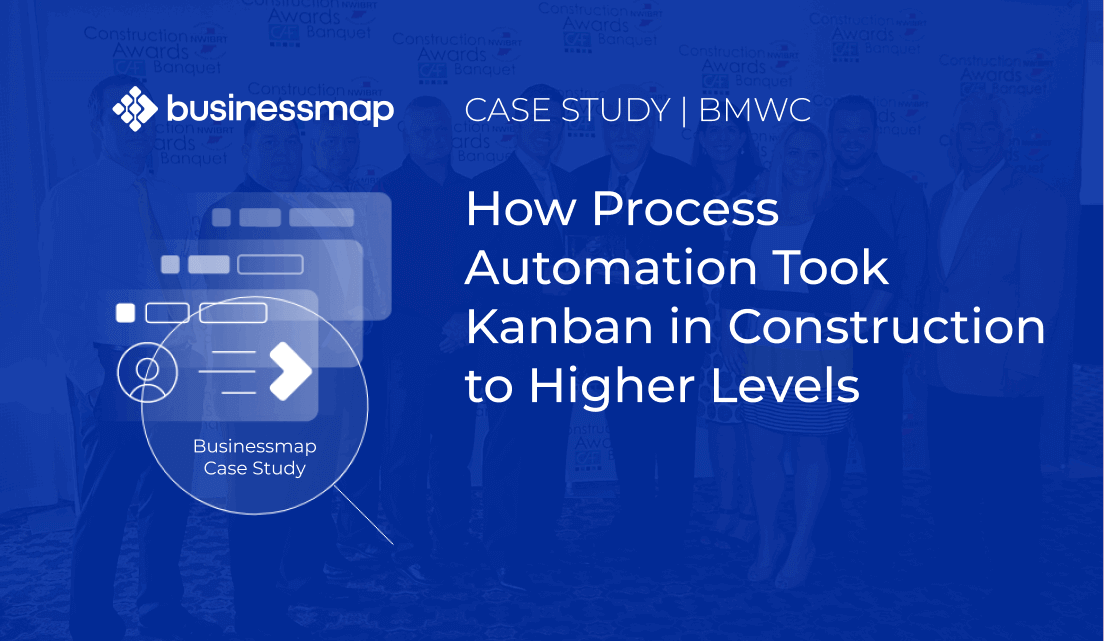
BMWC Constructors is an American construction company that tackles the world's toughest, most daunting industrial construction challenges. Mostly performing pipe fabrication and installation, they serve industries including Aerospace, Biotechnology, Pharmaceutical, Power Generation, Semiconductor, Oil and Gas Distribution, Refining, and Chemical companies.
For BMWC, a sustainable business means excellent customer relationships and continuous performance improvement. However, ineffective communication and the lack of visual/virtual project management solutions stood in their way of achieving those goals.
Challenges that Led to Change
Before the work management platform by Businessmap, communication between the Fabrication Shop and multiple job sites was accomplished via email and phone calls. Historical work tracking was done using Excel. There was little transparency and a lot of "He said, she said" which created confusion and difficulties at every stage of the shop drawing, piping fabrication, pipe installation, and quality control processes. Each job site was also somewhat disconnected from what the others were doing.
"Our main goal in adopting the Businessmap Software Platform was to create transparency and increase visual communication throughout our region."
Key Results
For BMWC, introducing Businessmap software has revolutionized its workflow and significantly increased regional transparency.
Want to achieve the same results?
Book a Product Demo
Optimized Efficiency
With the digital Kanban boards, team members are now able to communicate across multiple project sites very quickly and effectively, with everyone looking at the same data. Using the blocked card function and the comments tab, they can quickly share their constraints and keep each other updated on the resolution of these issues.
The data from the analytics panel showed that after the initial implementation of the software, the amount of finished work started increasing steadily, regardless of the number of cards entering the system. This is evidence that process visualization and efficient communication are speeding up delivery, even without making drastic organizational changes.
Better Flow Tracking
Initially starting with workflow visualization, as BMWC experienced the platform's capabilities, they developed further plans on how to use workflow tracking and the data it produces to gather reliable metrics to analyze workflow efficiency.
Looking at the trend chart for cycle time, for example, four months after the data collection started, they already saw a significant drop in cycle time.
Real-Time Collaboration
BMWC often has multiple project teams in a wide range of locations. Digital boards allowed seamless, real-time data communication across different geographical areas, easy updates, and changes.
Ensuring effective communication and real-time collaboration is often tightly related to creating an automated workflow that doesn't depend on each person's attention, memory, and presence to function smoothly. The product's Automation functionalities allowed BMWC to inform relevant teams or team members in real time about specific high-priority events occurring in the construction process without someone having to ring an alarm.
This way, new company standards were established by applying custom business rules.
Knowledge Sharing
"The software has created a new environment centered around communication and transparency in a visually appealing way that we haven't seen before."
- Ben Jackman
Fabrication Shop Coordinator
Download Case Study