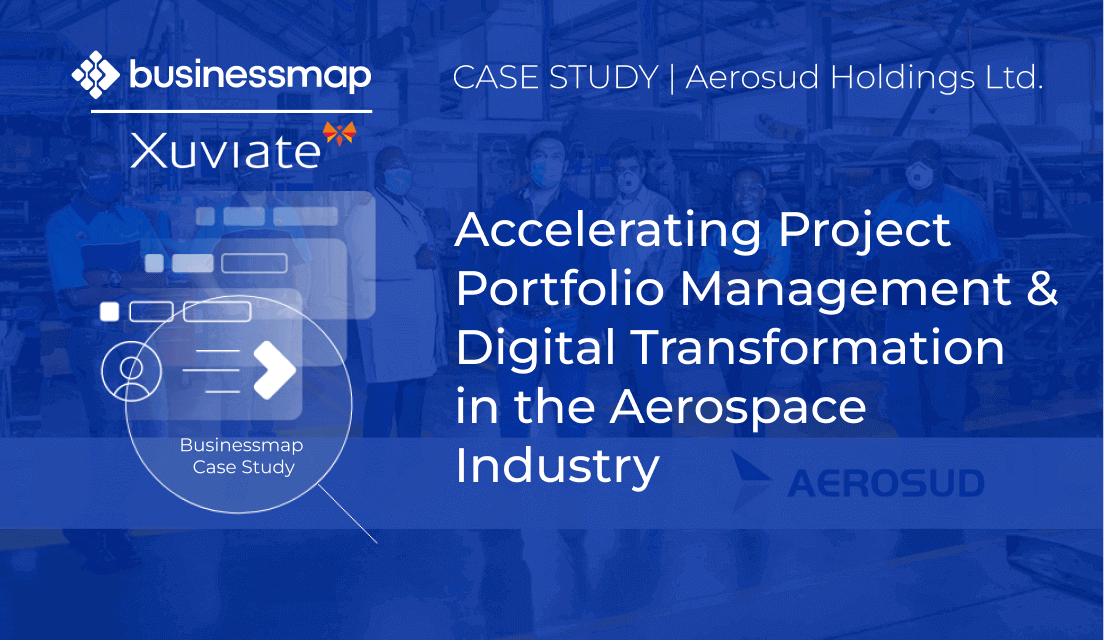
Aerosud Holdings Ltd. is an internationally recognized manufacturer of aircraft parts and assemblies from South Africa. They are a supplier of OEM aircraft brands such as Airbus, Boeing, BAE Systems, etc.
Initial Challenges
One of the main challenges that initially sparked the idea of adopting Lean/Agile was the slow response rates within the IT services area. Due to the lack of work transparency, the IT area had problems communicating expectations upfront, setting clear priorities, and escalating issues to the right stakeholders.
Doubling the ITSM Throughput with Kanban
Aerosud’s IT area started with physical Kanban boards on an individual level. After undergoing Kanban training, they realized that high levels of Work-In-Progress contribute to longer cycle times (based on Little’s Law) which made the team agree on limiting WIP on every individual board.
Due to this and other practices, the IT group doubled their throughput from 60 to around 120 tickets within 3 days!
Want to achieve the same results?
Book a Product Demo
Detaching From the Physical Boards
Even though the improvements were visible, the limitations of the individual boards soon became obvious.
For example, there was no way to create an automatic integration between Aerosud’s IT systems and the actual workflow. Realizing the need for business agility, Aerosud's management was also looking for a solution to scale the adoption of Kanban across multiple departments.
Maturing the Kanban Implementation
Managing IT Service Delivery and Automating Workflows
After going through online Kanban training and iterating on a few versions of a digital board in Businessmap (formerly Kanbanize), the IT group visualized multiple team workflows on a single board.
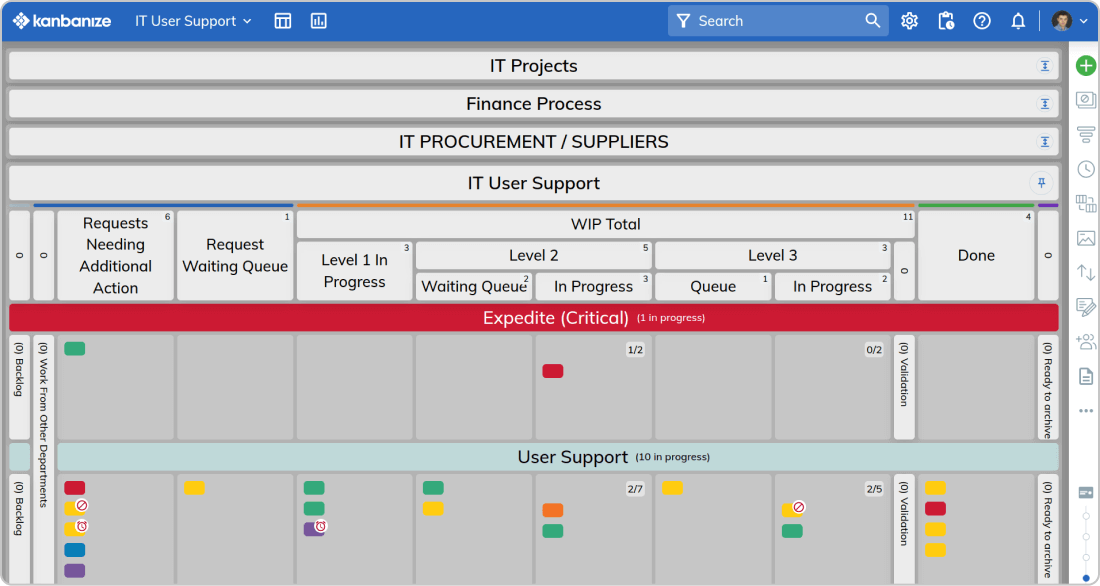
To visualize demand, Aerosud’s IT group used the platform's API to integrate their workflow with an external IT service desk portal.
Initiating an Engineering Project Portfolio Management Implementation
Looking for enhanced agility, Aerosud decided to apply flow management for projects in Engineering. The Engineering department implemented a board in their dedicated work management platform that visualizes the workflows of different service groups – Design, Mechanical, CNC, Professional Engineering, etc.
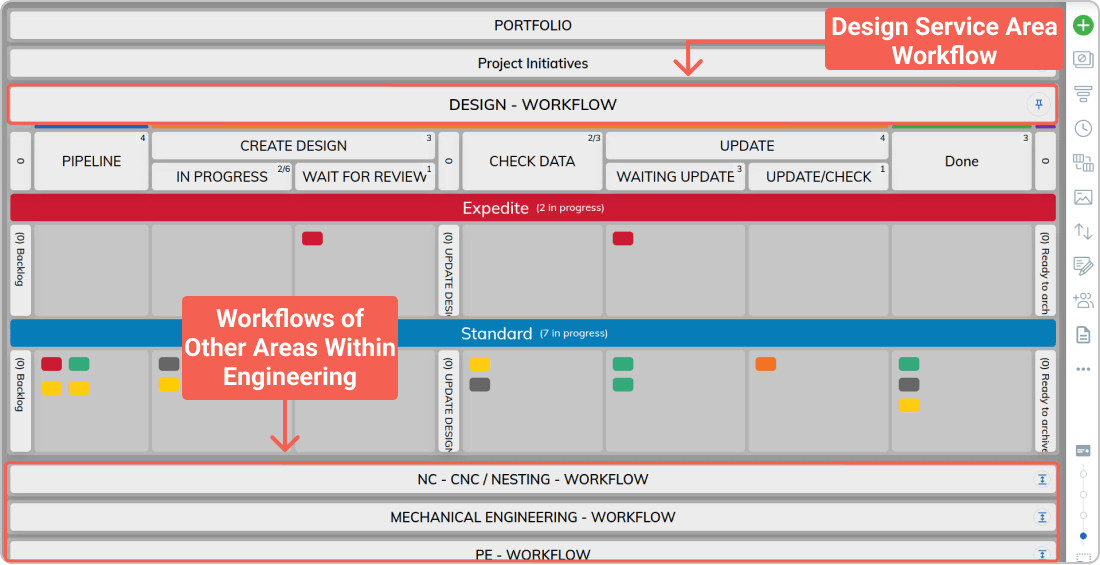
They also implemented the "Flight Levels” concept by Klaus Leopold for portfolio management (see more in the full version).
Measuring Performance, Key Results, and Integrating Power BI for Capacity Planning
Even though the Kanban implementation at Aerosud has matured significantly, leaders knew their ongoing Lean/Agile journey would be incomplete if they didn’t have the means to measure it. That’s why Aerosud turned to the Analytics capabilities in the Businessmap software, including a Power BI integration, which you can read more about in the document below.
Key Results
- Built a clear workflow structure through interconnected boards across departments.
- Gained capacity planning and allocation capabilities
- Collected data (impossible to measure with the physical boards) and improved planning efforts.
- And many more...
Download Case Study