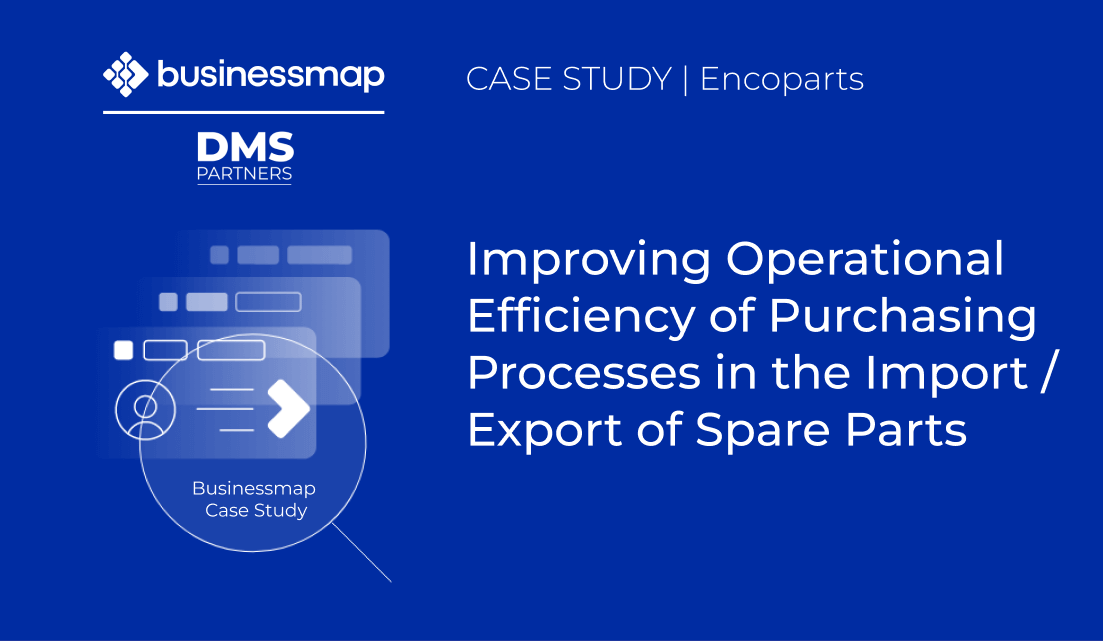
Introduction
Encoparts® was founded by highly specialized professionals with more than 20 years of experience in importing and distributing spare parts for the Yellow Line.
Challenges
As a distribution logistics company with a strong presence in the Americas and Australia, Encoparts® was dealing with a number of challenges in its International Purchasing (LLC-USA) Unit.
- Challenge #1 – High Complexity
- Challenge #2 – Customer dissatisfaction
- Challenge #3 – Low visibility of the process
- Challenge #4 – Bad communication
- Challenge #5 – Need for systemic vision and automated workflow
Enabling Workflow Transparency & Efficiency Through a Lean/Agile Transformation Journey
The Lean/Agile transformation journey in the Encoparts purchasing area was built around the introduction of the Kanban method, which happened through a concept known as STATIK (Systems Thinking Approach to Introducing Kanban).
Process Mapping & Other Lean/Agile Practices
To understand the current processes of the purchasing area, including their weak spots, the company underwent a series of theoretical training which led to the implementation of the Lean technique – Value Stream Mapping.
The technique represents a visual method for illustrating, analyzing, and improving the steps required to deliver a product or service. Through this concept, it was possible to determine what adds value to the processes but also uncover the non-value-adding steps and other deficiencies that limited the evolution of the service.
Teams prepared an actual breakdown of each of their most important steps in the process and visualized them for better clarity. The benefit of such a process map is that it helped them understand their value-adding and non-value-adding activities.
Want to achieve the same results?
Book a Product Demo
Accelerating The Lean/Agile Transformation
To bring the Value Stream Mapping technique into practice and get historical data for process metrics, Encoparts embraced a digital solution in the face of Businessmap. With its help, they built Kanban boards to visualize the entire end-to-end flow and gained the ability to analyze flow metrics for improvements.
In general, some of the most used features from the digital solution at Encoparts include:
- E-mail integration
- Comments
- Classes of service
- Output criteria for work items
- Workflow Management
- And more...
Key Results for Coordination and Flow Efficiency
Among the improvements that followed, post-implementation, Encoparts® highlighted 5 main points that proved most beneficial in the International Purchasing operations because of the Businessmap Software Platform implementation.
- Reduction of complexity
- Improved communication
- Better prioritization in customer service
- Process automation and visibility
- The introduction of metrics for performance evaluation/analysis of deviations/improvements
Key Takeaways
The main takeaway from the implementation is that Encoparts managed to improve its operational (flow) efficiency by almost 33%. There are other important improvements they've reported too.
Download the full case study to learn more.
Download Case Study