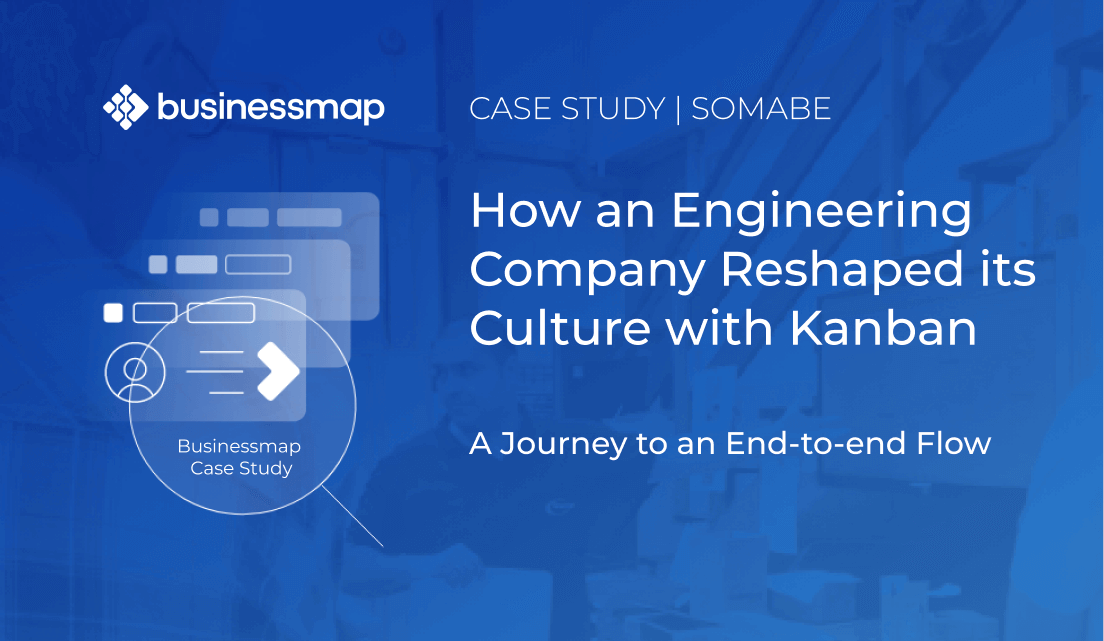
Introduction
Somabe is an industrial engineering company that designs and manufactures individual machines. Each machine order is different, and its development is managed as a project.
Six years ago, the company was facing several problems:
- Tasks were assigned verbally, and there was no transparency about their states.
- There was a lack of awareness of the actual capacity of each department.
- Planning was based on ad-hoc effort estimates, fixed in the budget, and must-meet.
- Work was moving through the departments as a wave of large batches.
- Problems were resolved thanks to heroic personal efforts, which, at some moments, created tension between people.
Initial Challenges
The situation was not sustainable. At that time, there was a change of management, and Aitor Eguren took the wheel of the company as General Manager.
To improve this situation, at first, Somabe decided to adopt Scrum. For a certain period, this approach worked at the team level. However, a year or so later, Aitor started realizing that although they were organized in departments, they needed to manage the entire workflow to improve the project outcome.
At the same time, it was necessary to break down the machine in assemblies to better manage their development and production and to reduce the large batches. Therefore, they choose to switch to Kanban and start visualizing work with physical Kanban boards. Gaining a better overview, Somabe's management realized the need for greater improvements in current work practices. Moving forward, they started evaluating digital Kanban tools that can help them introduce process improvements, achieve alignment on a company level, and bring business agility and robustness to the next level.
Key Results
“We decided to use Businessmap (formerly Kanbanize) because we find it so easy to design and modify our boards. This allows us to continuously improve our process at no cost of adapting the solution.
Developed a Work Breakdown Structure to Segment Complex Tasks into Smaller, More Manageable Portions
The Businessmap Software Platform helped Somabe break down work into smaller pieces by utilizing different card links options (parent, children, relative to one or multiple other Kanban cards).
Using these link types, Somabe achieved a hierarchical work-breakdown structure and introduced the Portfolio Kanban concept. 
Created an Advanced, Automated Workflow that Aids Task Assignment and Decision Making, Encouraging Cross-Team Collaboration
Starting to manage the work through interconnected Kanban systems allowed Somabe to create a more streamlined workflow and automate some of their routine actions with the help of the Business Rules Automation Engine or the so-called Runtime policies.
Want to achieve the same results?
Book a Product Demo
Gained Real-Time, Company-Wide Visibility of All Active Projects and Dependencies
Automating workflows, visualizing dependencies, and integrating the work management software with their ERP, CRM, BPM, and other engineering tools allowed Somabe to gain real-time visibility into the projects of the company. This new level of transparency made the real capacity of each department also visible at a glance and allowed for better management of potential workload and planning issues.
Created a Culture of Innovation, Learning, and Continuous Improvement
“The tool provided by Businessmap is the universal language of the entire company. Everyone understands and speaks it."
With its powerful analytics module, the software helped Somabe obtain an objective, data-based understanding of issues. This often demonstrated that problems were due to processes, not people, and encouraged a mentality of continuous improvement on all levels.
Download Case Study